Digital Fabrication
Additive vs Sustractive fabrication
This type of manufacturing allows the processes to be repeatable as many times as necessary. In turn, the complexity of the object does not have a significant impact on the cost of production. The possibilities within digital fabrication are not linked to the human scale.
Digital fabrication technologies can be divided into two large groups. On the one hand the additive fabrication and on the other the subtractive, each one of them presents certain limitations, advantages and disadvantages to the other.
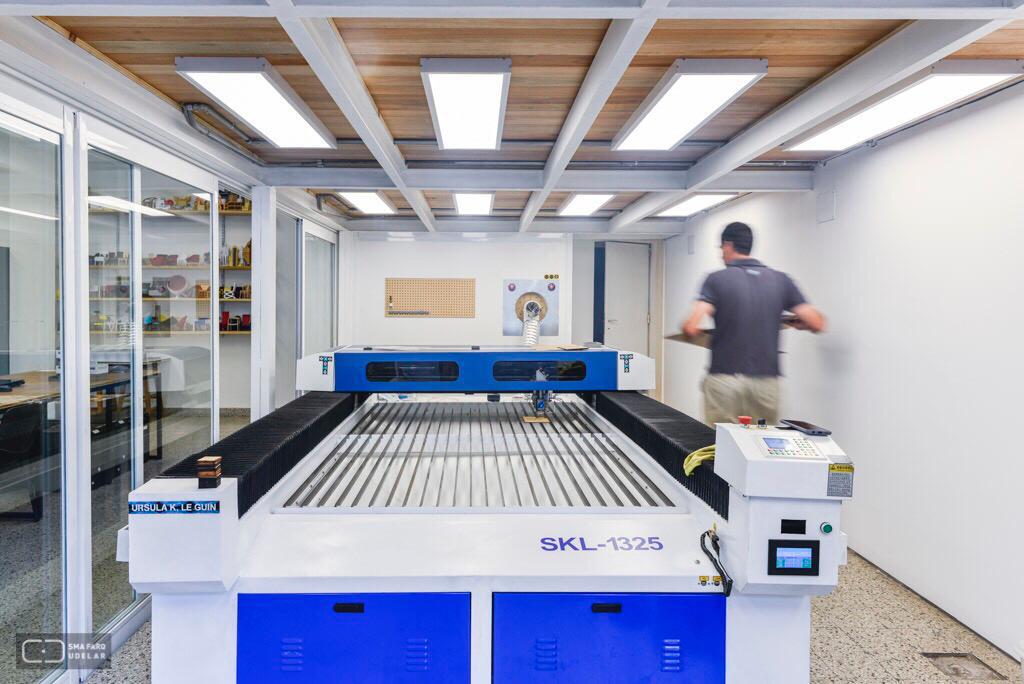
Aditive fabrication

Aditive fabrication is the type of digital manufacturing, which allows the construction of objects in three dimensions in a sequential way, during a process of adding material by layers. In many cases it uses heat to provide fluidity to the material used.
Advantages
- It does not generate waste of material in the process.
- It is possible to change the physical properties of the object.
- The interior is also designed.
- Wide range of machinable materials and it is expanding: polymers, ceramics, cement, metals, sand, chocolate….
Disadvantages
-
Expensive processes.
-
Very slow processes compared to massive processes technics, like injection.
-
In the case of 3D printing, they are limited to the dimensions of the printing bed.
-
Parts made from 3D printing often require some type of cleaning and finishing to achieve their final properties and appearance. On many occasions, the model requires the use of support structures, which are removed once printing is finished. These can be made of the same material as the impression or made of materials that dissolve in water, which allows for easier removal and a better finish on the final piece.
Technologies
- 3D printing:
Polymers: Fused Deposition Modeling (FDM), Stereolithography Sintering (SLA), Digital Light Processing (DLP), Selective Laser Sintering (SLS).
Metals: Direct Metal Laser Sintering (DMLS), Electron Beam Melting (EBM), Binder Jetting, and Selective Laser Melting (SML).
Sustractive fabrication
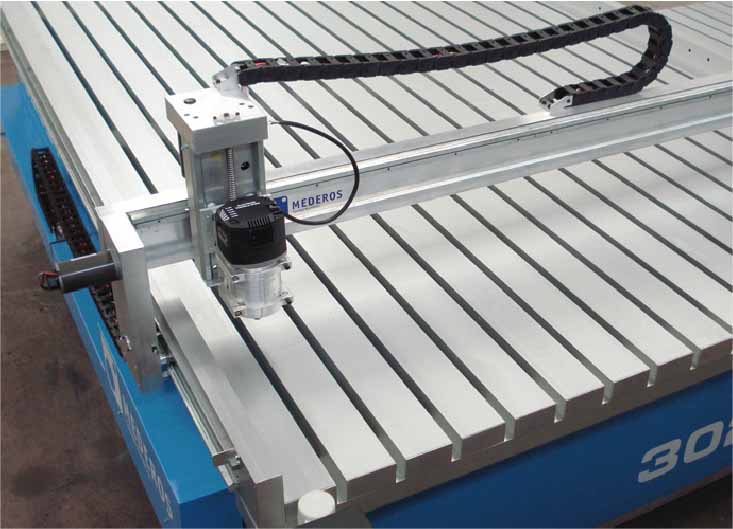
Sustractive fabrication gathers all those forming operations in which the excess material is removed from an initial work piece. The most important processes in this category are machining operations such as turning, drilling, milling, and grinding. Non-traditional processes are used because they use lasers, electron beams, chemical erosion, electrical discharges, or electrochemical energy to remove material.
Advantages
- In general, it uses the same materials as traditional techniques.
- Higher precision parts are obtained than additive manufacturing methods.
- Repeatable process.
- Efficient use of material (nesting). The optimization of the cuts saves material.
Disadvantages
- Generate waste material.
Technologies
- Laser cutting
- CNC (drilling machine, lathe, panel saw, router)
- Water jet cutting
- Plasma cutting
- Electrical discharge machining (EDM)
Basic terminology
To carry out the fabrication of any object through any of the technologies mentioned above, it is essential to understand and manage the different languages so that the machines, operators and software correctly interpret the projects.
CAD
Computer Aided Design
The file containing the design to be manufactured. It is important that the design does not contain double lines, curves without closing or elements that do not touch each other.
Software: Autocad, Illustrator, Corel, etc.
CAM
Computer Aided Manufacturing
Translates the CAD file into a set of instructions that the machine can interpret: CAM= translator. This file must contain the specific elements/parameters that the machine will need for manufacturing: speeds, intensity, times, etc. For this reason, the plans must express not only what is necessary for the machine but also what is necessary for the operator who will configure the machine.
Software: Cura, Fusion 360, etc.
CNC
Computer Numerical Control
It is used to create programming instructions for a computer to control a certain machine/tool. CNC is related to the manufacturing process and improves automation as well as flexibility.